In today’s rapidly changing manufacturing environment, efficiency and precision are key to staying ahead of the competition. Manufacturers are no longer just producing goods; they are trying to produce them smarter and more efficiently than ever before. This is where the world of custom software development meets the manufacturing industry. But what exactly is Manufacturing ERP and why is it such an important resource for modern manufacturing companies? In this article, we’ll delve into the heart of manufacturing ERP, exploring its features, benefits and the types of companies that stand to gain the most from implementing it.
What is manufacturing ERP software?
Manufacturing ERP (Enterprise Resource Planning) software is a specialized software solution designed to meet the unique needs of manufacturing industry. It integrates and improves various business processes within a manufacturing organization, including production, inventory management, quality control, demand forecasting and supply chain management. By providing a centralized platform for management and data analysis, Manufacturing ERP helps manufacturers optimize operations, reduce costs, improve product quality and make data-driven decisions. The technology is a key tool in the modern manufacturing industry, enabling companies to stay competitive, efficient and responsive to market needs.
What are the benefits of manufacturing ERP?
The benefits of an ERP system for manufacturing are numerous. They include increased productivity, reduced operating costs, improved quality control, accurate demand forecasting, streamlined supply chain management and real-time access to critical data. Manufacturing ERP (Enterprise Resource Planning) software offers countless benefits, making it an invaluable tool for modern manufacturing companies. Let’s take a look at some of the key advantages, backed by real-world examples:
Increased efficiency
Manufacturing ERP systems play a key role in optimizing production schedules and resource allocation in manufacturing organizations. This optimization, in turn, leads to significantly reduced lead times and faster order fulfillment. By streamlining and automating various production processes, these systems allow for better coordination of resources and help ensure that each task is performed at peak efficiency. As a result, companies can meet customer demands faster, enhancing their reputation and competitiveness in the market.
Reduction in operating costs
Another major benefit of implementing a manufacturing ERP system is the reduction of operating costs. ERP software improves various processes, automates repetitive and time-consuming manual tasks, and increases visibility into operational expenses. This increased visibility allows organizations to make informed decisions on cost reduction strategies, both in terms of direct labor costs and indirect operating costs. With a comprehensive overview of their expenses, companies can identify areas where savings can be achieved, helping to improve profitability.
Enhanced quality control
Quality control is a critical aspect of manufacturing, and ERP systems for manufacturing play a significant role in this area as well. These systems provide real-time quality control and monitoring tools, enabling manufacturers to closely monitor production processes and product quality. By reducing the risk of defects and waste, Manufacturing ERP ensures that products leaving the production line meet the required quality standards. This not only increases customer satisfaction, but also reduces costs associated with rework and waste disposal.
Accurate demand forecasting
In today’s dynamic market environment, accurate demand forecasting is a key success factor for manufacturing companies. Manufacturing ERP systems use a data-driven approach and advanced demand forecasting capabilities to provide insight into changing market conditions. This enables manufacturers to quickly adapt to changes in customer demand, ensuring that production is aligned with actual requirements. By reducing the possibility of overproduction or underproduction, ERP systems contribute to better inventory management and financial savings.
Streamlined supply chain management
Effective supply chain management is critical to manufacturing success, and ERP systems for manufacturing facilitate this through better coordination and collaboration across the supply chain. By offering real-time visibility into supply chain processes, ERP systems help optimize inventory levels, improve demand forecasting and strengthen collaboration with suppliers. This provides a smoother and more flexible supply chain, reducing lead times and increasing overall efficiency.
Access to real-time data
Manufacturing ERP systems provide companies with real-time access to data on various aspects of their operations, such as inventory levels, production status and customer orders. This access to real-time data is invaluable for quick decision-making and the ability to respond to changing market conditions quickly. Manufacturers can make informed decisions about production, resource allocation and fulfillment of customer orders, resulting in more agile and competitive operations. In addition, it enables them to identify potential problems when they occur and take immediate corrective action, further improving operational efficiency and customer satisfaction.
Why should your company invest in ERP for manufacturing?
Investing in an ERP system for manufacturing is a strategic move that brings significant returns. In today’s dynamic business landscape, where efficiency, productivity and cost control are the most important, an ERP system for manufacturing streamlines processes, reduces operating costs and improves product quality. This enables the company to meet customer demands, stay ahead of the competition and make data-driven decisions. Manufacturing ERP integration increases automation and provides real-time insight into production, inventory and supply chain, improving operational efficiency and ensuring competitiveness. This investment ensures the long-term success and sustainability of the company, regardless of its size or manufacturing sector.
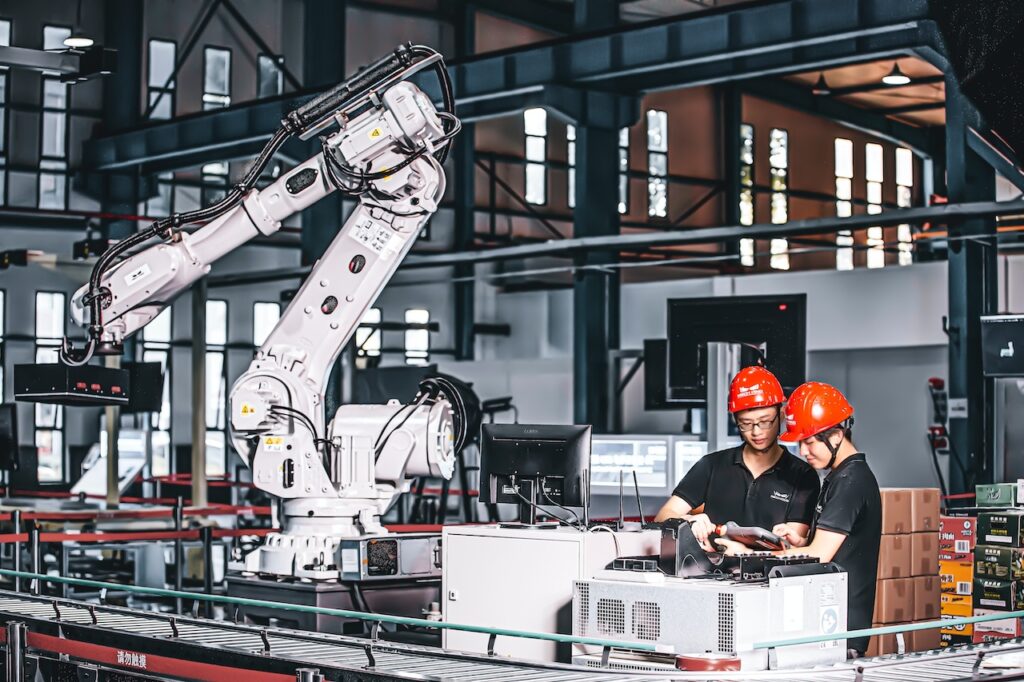
What are the different types of ERP implementation?
ERP (Enterprise Resource Planning) implementations vary based on a company’s unique needs, IT infrastructure, and strategic objectives. There are several common types of ERP implementation approaches:
Local ERP system
When a local ERP system is implemented, the software and hardware infrastructure are deployed and maintained at the company’s physical location. This approach provides full control and customizability of the ERP system, but requires a significant upfront capital investment in hardware and software licenses. It also requires an in-house IT team to manage maintenance and upgrades. Local ERP is preferred by some organizations that have specific security or compliance requirements and want full control over their data.
Cloud-Based ERP
Cloud ERP solutions are hosted on remote servers by third-party providers. They offer scalability, flexibility and lower capital expenses because there is no need for on-site servers. Cloud ERP enables remote access, facilitating collaboration and data sharing between geographically dispersed teams. Updates and maintenance are managed by the service provider, reducing the workload on IT. This approach is becoming increasingly popular because of its flexibility and availability.
Hybrid ERP
Hybrid ERP solutions combine local and cloud-based systems. Companies can keep some critical processes in-house while moving less sensitive functions to the cloud. This hybrid approach offers a balance of control and scalability, meeting the needs of organizations with specific security requirements or integration of legacy systems.
Industry-Specific ERP
Some ERP solutions are designed with specific industries in mind, such as manufacturing, healthcare or retail. These industry-specific ERP systems come with pre-configured functions and processes tailored to the unique needs of the sector, saving time and effort in customization. For example, a manufacturer may opt for an industry-specific ERP system to streamline production, quality control and supply chain processes.
Open Source ERP
Open source ERP solutions provide flexibility and customization options. They allow companies to access and modify the source code to meet their specific requirements. While open source ERP solutions offer cost-effective solutions, they can require significant resources for development and support. This approach is popular with organizations looking for extensive customization and willing to invest in development resources.
Each ERP implementation type has its advantages and drawbacks, making the choice dependent on the organization’s needs, budget, and long-term strategies. Custom software development can further adapt and enhance the chosen ERP implementation to align perfectly with a company’s unique processes and objectives. Deciding on the most suitable ERP implementation type is a crucial step in maximizing the benefits and ROI of the ERP system.
What kind of companies need manufacturing ERP?
Manufacturing ERP is essential for a variety of companies in different industries, serving organizations involved in manufacturing, assembly or processing. Whether you’re a small or medium-sized enterprise (SME) or a large corporation, if you want to optimize operations, improve quality control, improve your supply chain and make data-driven decisions, ERP for Manufacturing is customized to meet your needs. It is especially beneficial for manufacturers who want to reduce operating costs, increase productivity and ensure product quality in an increasingly competitive market, whether they focus on discrete manufacturing, process manufacturing or a combination of both.